1.线圈电流密度不宜过大或过小:
电机线圈具有一定的电阻.当电流通过线圈时就产生损耗.绕组温升高,电机设计希望减小电阻,以减小损耗,提高效率.加粗线径,降低电流密度可以减电阻,但会线圈材料用量增加.由于槽面积的加大,引起铁心磁密增加,使电机的励磁电流和铁损增加.通常感应电机j取3~7A/mm2
(槽面积大也就是芯片设计时铁心槽孔大),对于大电机及封闭式电机取小值.对于小电机及开启式电机则取大值。
2.电机铁心的磁通密度不宜过高或过低.
当铁心材料,频率和硅钢片厚度一定时铁损决定于磁通密度的大小,磁通密度过高使铁损增加,电机效率降低,铁心发热使电机温升增高.并由于励磁安匝增加电机功率因数降低,所以铁心的磁通密度不宜过高,尽量避免用在磁化曲线的过饱和段,小型电机一般不超过1.55T。磁密过低则使电机材料用量增加,成本提高,芯片齿部窄,磁密高即槽入线的空位大也就是铁心槽孔大反之.
3.电机槽满率不宜过高或过低
所滑槽满率是指槽内导线的面积和槽有效面积之比,即N2d,N为导线并绕根散l=为每槽导体数;d为导线绝缘后外径Is,为槽有效面积(为槽面积减击槽绝缘所占面积)。槽满率大,表示槽内填充紧密,槽满率小,表示槽内填充松散。就电机用料的充分利用和运行性能来说,槽辨率最为好。但过高嵌线困难,劳动量及工时增加,容易损伤绝缘。
一般取75~85% 。槽满率低,电机运行时导线在槽内松动,易损伤绝缘。此外槽内空隙多,由于空气导热差,影响线圈的散热使电机温升增高。
4.电机槽形的设计尽可能选用平行齿梯形槽
硅钢片工作在磁化曲线的饱和段,单位长度励磁消耗的安匝数随磁通密度的增加而大量增加。为了合理充分利用电机内部空间,电机设计时总是使硅钢片比较饱和。如果采用梯形齿,则齿的窄部由于磁通密度大,励磁安匝数大量增加,电机的功率因数降低。如果采用平行齿.则沿齿部长度内磁通密度均匀,励磁消耗的安匝数大为减少。槽形边缘不要有尖角,尽量用圆底槽,由于圆槽铸铝时填充好,并做模方便.定子芯片嵌线容易。
尽量用圆底槽代替平底槽,圆底槽的优点:
A.圆底槽能改善导线的填充情况.槽绝缘不易损坏,在槽满率相同的情况下,圆底槽嵌线比平底槽容易。
B.转于铸铝时,圆底槽比平底槽铝水填充情况好。
C. 圆底槽比平底槽便于模具制造。
5.电机槽口宽度不宜过大
电机槽口太小,下线困难。电机槽口太大.使气隙磁通分布不均,齿谐波增大.附加损耗增加。半闭口槽的槽口宽度一般为2~3根导线的直径,约为3.5mm。低压成形线圈采用槽内四个元件边的半开口槽结构,使其槽口宽度减少为槽宽的一半。
6.定子槽数不要太多或太小
异步电动机定子槽数多,磁动势、电动势波形好.附加损耗小,电机效率高。槽数多,还使线圈和铁心的接触面积增加,线圈散热好,温升低。但槽数多,铁心齿部过窄,冲压变形大,工艺性差。槽数多还使模具制造成本增加,有关电机设计的问题,线圈制造及下线工时增加,一般说来.定子槽数多、电机性能好.但成本高。
7.异步电机气隙大,磁阻大,励磁安匝数多,使电机励磁电流增大,电机功率因子降低,但气隙大使谐波磁场减弱,电机附加损耗降低,,气隙太小易引起定转子扫膛,以及由于附加损耗增加而使电机效率降低。
8.异步电机转子扭斜可以使转子导条沿轴向的谐波电势相位不同而被削弱,从而减少了附加同步转矩,及附加异步转矩,降低电机附加损耗,提高效率,降低噪音,振动.
9.单层绕组不要用于容量较大的电机,容量较小的电机不要双层绕组.
10大电机不宜用铝合金做支架由于刚度,强度差些
11.转轴上尽量避免用不同宽的键槽(即介子槽)轴芯二级位应倒圆角.
12电机两端都用滚动轴承时轴向不要卡死.因为电机运行时转轴的散热比定子支架差,温升高些,转轴的热膨涨要大于定子部件,和支架,机座.转轴就不能自由膨胀,所以一般加波浪介子加啤令盖.
13.转轴和转子芯片配合的长度不要太长.(轴芯中间部分可以缩小解决)
14.带滚动轴承结构的不要使电机转子产生轴向窜动.(所以啤令内加波浪介子)滑动轴承的在转子前端加弯介子 手提吸尘机的不带弯介子是前端是E介子结构虚位控制很小0.1~0.4mm
15.电机的定,转子铁心不要错位,错位不利的原因a:错位相当于空气隙有效面积减小,励磁电流增大,功率因子降低.,还使定子电流大定子铜损大,效率低.温升高.
B:转子受到一个轴向力加快轴承磨损.增大电机的噪音和振动.(但有些成品运行向前端一个方向常常磨一端轴承此时故意错位)c:影响电机的正常通风.
16.注意异步电机转子铸铝质量(可用硫酸化解芯片看)
17.引线不要过细如果过细的引线容易绝缘老化通常导体电流密度取4~6A/mm2小电机取大值.大电机取小值.
18.电机起动电流一般是额定电流的6倍左右,所以不要频繁起动,堵转的电流菲士通常是额定电流的2.5~3倍. 电流菲士需200%的电流才能冲断.
19.转子临界转速应大于1.2倍或小于0.8倍的额定转速以免发生共振.
20.电机干燥时应避免温度急剧升高.过分潮湿的绕组,应避免用通入电流的方法进行干燥.
21.定子槽楔不要高于铁芯内圆
22.拆卸轴承入轴承应当加力于啤令内圈,不能受力啤令外圈和钢球位.
23.多粉尘场所不要用防护式电机应用封闭式电机.(但封闭式电机不易散热.
24.不要便电机在电源频率过低下运行.电源电压一定时,频率下降使磁通增加,电机设计一般使硅钢片工作在磁化曲线的饱和区,磁通增加使励磁电流增加较多,功率因子下降,电机电流增大铜损增加,效率下降,频率下降还使电机转速下降.风量减少,散热困难,电机温升增高.电源频率下降不但电机输出功率减少,而且使各项性能变坏.额定频率不能超过1%
25.不要使异步电机的电源电压过高或过低 电压过低电机磁通减少,电机转矩则与电压平方成正比下降.造成电起动困难,电机负载不变时电机电流增加,损耗加大,温升增高,长时间低压运行可能使电机烧毁.
26.换向器和碳刷的摩擦噪声.是因为a换向器表面加工精度不够和粗糙度较差.b.碳刷和刷盒间隙过大.c碳刷弹簧弹力失效.另外换向器表面有杂物易产生火花.电机设计需要注意的事项
1.线圈电流密度不宜过大或过小:
电机线圈具有一定的电阻.当电流通过线圈时就产生损耗.绕组温升高,电机设计希望减小电阻,以减小损耗,提高效率.加粗线径,降低电流密度可以减电阻,但会线圈材料用量增加.由于槽面积的加大,引起铁心磁密增加,使电机的励磁电流和铁损增加.通常感应电机j取3~7A/mm2
(槽面积大也就是芯片设计时铁心槽孔大),对于大电机及封闭式电机取小值.对于小电机及开启式电机则取大值。
2.电机铁心的磁通密度不宜过高或过低.
当铁心材料,频率和硅钢片厚度一定时铁损决定于磁通密度的大小,磁通密度过高使铁损增加,电机效率降低,铁心发热使电机温升增高.并由于励磁安匝增加电机功率因数降低,所以铁心的磁通密度不宜过高,尽量避免用在磁化曲线的过饱和段,小型电机一般不超过1.55T。磁密过低则使电机材料用量增加,成本提高,芯片齿部窄,磁密高即槽入线的空位大也就是铁心槽孔大反之.
3.电机槽满率不宜过高或过低
所滑槽满率是指槽内导线的面积和槽有效面积之比,即N2d,N为导线并绕根散l=为每槽导体数;d为导线绝缘后外径Is,为槽有效面积(为槽面积减击槽绝缘所占面积)。槽满率大,表示槽内填充紧密,槽满率小,表示槽内填充松散。就电机用料的充分利用和运行性能来说,槽辨率最为好。但过高嵌线困难,劳动量及工时增加,容易损伤绝缘。
一般取75~85% 。槽满率低,电机运行时导线在槽内松动,易损伤绝缘。此外槽内空隙多,由于空气导热差,影响线圈的散热使电机温升增高。
4.电机槽形的设计尽可能选用平行齿梯形槽
硅钢片工作在磁化曲线的饱和段,单位长度励磁消耗的安匝数随磁通密度的增加而大量增加。为了合理充分利用电机内部空间,电机设计时总是使硅钢片比较饱和。如果采用梯形齿,则齿的窄部由于磁通密度大,励磁安匝数大量增加,电机的功率因数降低。如果采用平行齿.则沿齿部长度内磁通密度均匀,励磁消耗的安匝数大为减少。槽形边缘不要有尖角,尽量用圆底槽,由于圆槽铸铝时填充好,并做模方便.定子芯片嵌线容易。
尽量用圆底槽代替平底槽,圆底槽的优点:
A.圆底槽能改善导线的填充情况.槽绝缘不易损坏,在槽满率相同的情况下,圆底槽嵌线比平底槽容易。
B.转于铸铝时,圆底槽比平底槽铝水填充情况好。
C. 圆底槽比平底槽便于模具制造。
5.电机槽口宽度不宜过大
电机槽口太小,下线困难。电机槽口太大.使气隙磁通分布不均,齿谐波增大.附加损耗增加。半闭口槽的槽口宽度一般为2~3根导线的直径,约为3.5mm。低压成形线圈采用槽内四个元件边的半开口槽结构,使其槽口宽度减少为槽宽的一半。
6.定子槽数不要太多或太小
异步电动机定子槽数多,磁动势、电动势波形好.附加损耗小,电机效率高。槽数多,还使线圈和铁心的接触面积增加,线圈散热好,温升低。但槽数多,铁心齿部过窄,冲压变形大,工艺性差。槽数多还使模具制造成本增加,有关电机设计的问题,线圈制造及下线工时增加,一般说来.定子槽数多、电机性能好.但成本高。
7.异步电机气隙大,磁阻大,励磁安匝数多,使电机励磁电流增大,电机功率因子降低,但气隙大使谐波磁场减弱,电机附加损耗降低,,气隙太小易引起定转子扫膛,以及由于附加损耗增加而使电机效率降低。
8.异步电机转子扭斜可以使转子导条沿轴向的谐波电势相位不同而被削弱,从而减少了附加同步转矩,及附加异步转矩,降低电机附加损耗,提高效率,降低噪音,振动.
9.单层绕组不要用于容量较大的电机,容量较小的电机不要双层绕组.
10大电机不宜用铝合金做支架由于刚度,强度差些
11.转轴上尽量避免用不同宽的键槽(即介子槽)轴芯二级位应倒圆角.
12电机两端都用滚动轴承时轴向不要卡死.因为电机运行时转轴的散热比定子支架差,温升高些,转轴的热膨涨要大于定子部件,和支架,机座.转轴就不能自由膨胀,所以一般加波浪介子加啤令盖.
13.转轴和转子芯片配合的长度不要太长.(轴芯中间部分可以缩小解决)
14.带滚动轴承结构的不要使电机转子产生轴向窜动.(所以啤令内加波浪介子)滑动轴承的在转子前端加弯介子 手提吸尘机的不带弯介子是前端是E介子结构虚位控制很小0.1~0.4mm
15.电机的定,转子铁心不要错位,错位不利的原因a:错位相当于空气隙有效面积减小,励磁电流增大,功率因子降低.,还使定子电流大定子铜损大,效率低.温升高.
B:转子受到一个轴向力加快轴承磨损.增大电机的噪音和振动.(但有些成品运行向前端一个方向常常磨一端轴承此时故意错位)c:影响电机的正常通风.
16.注意异步电机转子铸铝质量(可用硫酸化解芯片看)
17.引线不要过细如果过细的引线容易绝缘老化通常导体电流密度取4~6A/mm2小电机取大值.大电机取小值.
18.电机起动电流一般是额定电流的6倍左右,所以不要频繁起动,堵转的电流菲士通常是额定电流的2.5~3倍. 电流菲士需200%的电流才能冲断.
19.转子临界转速应大于1.2倍或小于0.8倍的额定转速以免发生共振.
20.电机干燥时应避免温度急剧升高.过分潮湿的绕组,应避免用通入电流的方法进行干燥.
21.定子槽楔不要高于铁芯内圆
22.拆卸轴承入轴承应当加力于啤令内圈,不能受力啤令外圈和钢球位.
23.多粉尘场所不要用防护式电机应用封闭式电机.(但封闭式电机不易散热.
24.不要便电机在电源频率过低下运行.电源电压一定时,频率下降使磁通增加,电机设计一般使硅钢片工作在磁化曲线的饱和区,磁通增加使励磁电流增加较多,功率因子下降,电机电流增大铜损增加,效率下降,频率下降还使电机转速下降.风量减少,散热困难,电机温升增高.电源频率下降不但电机输出功率减少,而且使各项性能变坏.额定频率不能超过1%
25.不要使异步电机的电源电压过高或过低 电压过低电机磁通减少,电机转矩则与电压平方成正比下降.造成电起动困难,电机负载不变时电机电流增加,损耗加大,温升增高,长时间低压运行可能使电机烧毁.
26.换向器和碳刷的摩擦噪声.是因为a换向器表面加工精度不够和粗糙度较差.b.碳刷和刷盒间隙过大.c碳刷弹簧弹力失效.另外换向器表面有杂物易产生火花.
共2条
1/1 1 跳转至页
电机设计需要注意的事项(zt)
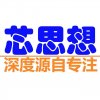
只看楼主 1楼
关键词: 电机
共2条
1/1 1 跳转至页
回复
有奖活动 | |
---|---|
【EEPW电子工程师创研计划】技术变现通道已开启~ | |
发原创文章 【每月瓜分千元赏金 凭实力攒钱买好礼~】 | |
【EEPW在线】E起听工程师的声音! | |
“我踩过的那些坑”主题活动——第001期 | |
高校联络员开始招募啦!有惊喜!! | |
【工程师专属福利】每天30秒,积分轻松拿!EEPW宠粉打卡计划启动! | |
送您一块开发板,2025年“我要开发板活动”又开始了! | |
打赏了!打赏了!打赏了! |
打赏帖 | |
---|---|
多组DCTODC电源方案被打赏50分 | |
【我踩过的那些坑】STM32cubeMX软件的使用过程中的“坑”被打赏50分 | |
新手必看!C语言精华知识:表驱动法被打赏50分 | |
【我踩过的那些坑】杜绑线问题被打赏50分 | |
【我踩过的那些坑】STM32的硬件通讯调试过程的“坑”被打赏50分 | |
【我踩过的那些坑】晶振使用的问题被打赏100分 | |
【我踩过的那些坑】电感选型错误导致的处理器连接不上被打赏50分 | |
【我踩过的那些坑】工作那些年踩过的记忆深刻的坑被打赏10分 | |
【我踩过的那些坑】DRC使用位置错误导致的问题被打赏100分 | |
我踩过的那些坑之混合OTL功放与落地音箱被打赏50分 |